Virgin Galactic Spaceship Desigen Reveal
Virgin Technology Summit
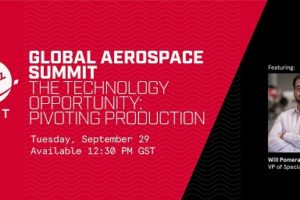
The Virgin Technology summit is a two event that starts today follow this link to join virtually:
https://hopin.to/events/global-aerospace-summit
The Virgin Technology summit is a two event that starts today follow this link to join virtually:
https://hopin.to/events/global-aerospace-summit